This article is about developing a custom WMS app (warehouse management system).
We’ll explain what warehouse management software is, and how warehouse automation reduces costs. Further, we’ll talk about the reasons why choose custom build warehousing apps, WMS features, and what should be kept in mind while creating a warehouse management system app.
What is warehouse management software?
Warehouse management includes activities related to warehouse processes from when goods enter a warehouse until they move out. Basically, it includes such warehouse activities as receiving, storing, tracking, picking, packing, and shipment.
The purpose of a WMS (warehouse management system or software) is warehouse management automation. It helps to ensure that goods and materials move through warehouses in the most efficient and cost-effective way.
It usually includes web admin part and mobile application for workers integrated with other 3rd party platforms and services so that the business has a unified management system.
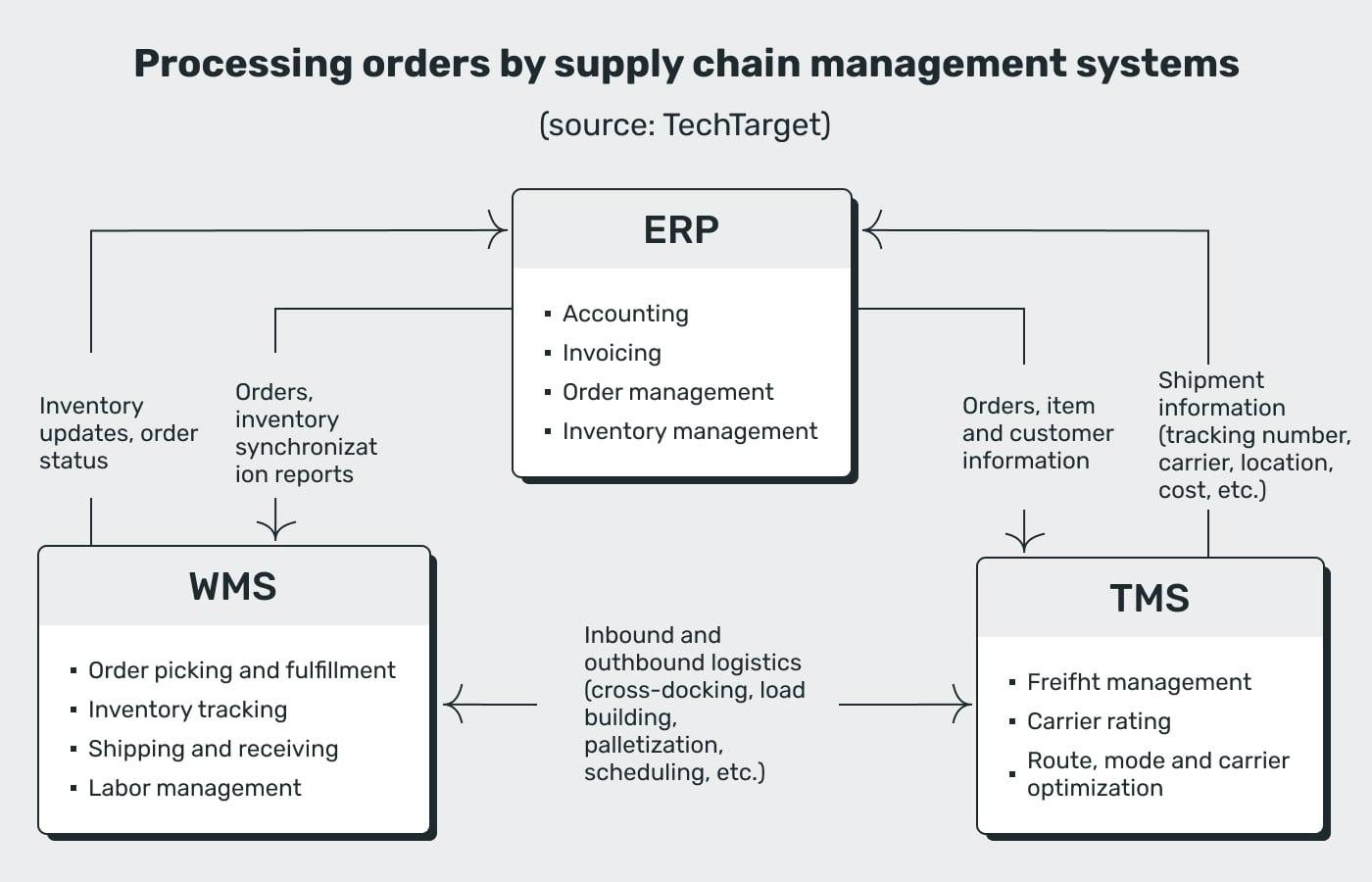
Why automation is needed in a warehouse?
- Reduces labor costs: less time spent on warehouse management, fewer specialists needed.
- Eliminates errors in picking and shipping goods: removing manual data input and the human factors.
- Increases revenue thanks to optimized inventory operations.
- Reduces cases of theft and loss of goods.
- Provides real-time visibility and analytics: the most current information on activities like orders, shipments, receipts, and any movement of goods.
Discover how automation can transform your operations! Get in touch with us!
Contact usWhy develop a custom warehouse app?
There are multiple off-the-shelf solutions available on the market like Dynamics 365, Microsoft, Salesforce, and some others. However, sometimes they do not fit the business needs properly. In this case, developing a custom application for managing warehouses is more reasonable.
- Cost. For small and medium businesses a high-quality ready-made warehouse management software may cost a pretty penny. The costs usually include sign-up, separate subscriptions for each specialist, and even contractors. Furthermore, to make the most of such software, it is required to set up, customize and support it properly which also adds additional expenses. It may seem that a custom WMS app costs more, but in the long run, the ROI of custom-made solutions for such companies is higher.
- Functionality. Despite the wide functionality available, it might be a challenging task to find one warehouse app which can cover your business needs. In the case of narrow purposed tools for various steps like yard management (parking, entrance to the loading/unloading dock, etc.), you’ll need to select several providers and integrate them with each other which means more expenses and potential problems. Your best option is a custom-developed WMS app in the following situations: if the existing software can’t satisfy your needs in terms of functionality, you require a specific functionality like managing perishable goods or generating custom reports, or you are looking for advanced features like AI-driven insights.
- Integrations. If you need to integrate warehouse management software with complex or legacy systems or you already have some part of the functionality. For example, a business may have a web application for warehouse managers and needs to develop a mobile application for workers which will be integrated with each other.
WMS app features
A WMS consists of several parts or applications. As a rule, there are two apps — a mobile warehouse app for workers and a web and/or mobile application for managers. In this article, we will focus primarily on the warehouse mobile app for workers.
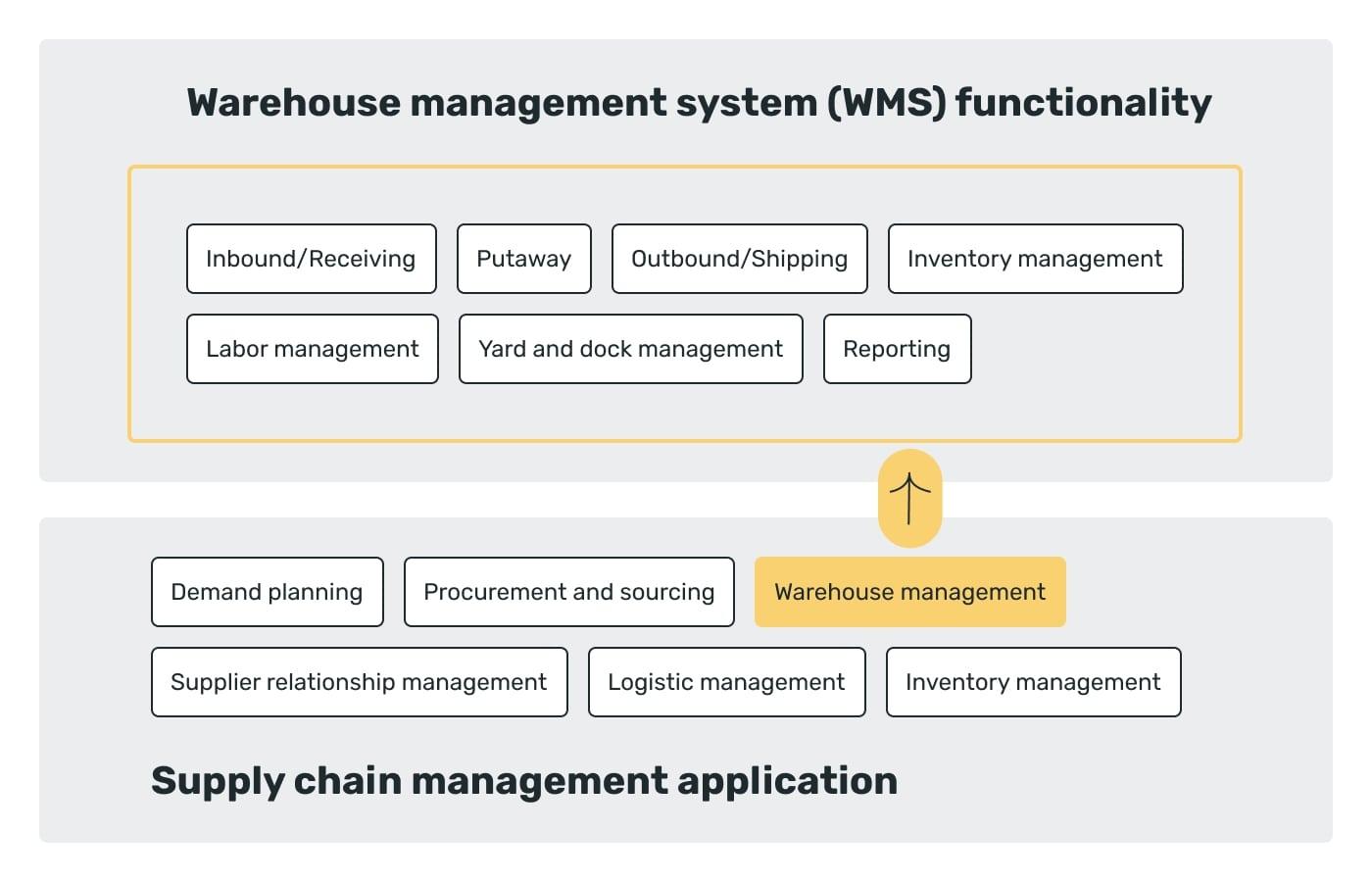
Inbound
Inbound functions refers to the activities related to receiving and validating items. At this stage, it is important to check if the goods received are right in terms of quantity and quality. For custom warehousing apps it is possible to create rules to spot mismatches and take the appropriate steps.
- Scan Purchase Order (PO) number / barcode (EAN) or RFID or it may be entered manually if there is no built-in scanner.
- Select item quantity.
- Display and edit information of a specific Item Number (EAN): PO, item name, quantity, unit of measure/type, size, color, SKU, etc.
- Confirm or cancel item received: if the Item Number is confirmed it will be added to the warehouse's inventory.
- Load over-receiving or under-receiving: automatic notifications informing about the mismatch between the initially announced quantity and the number of goods actually received. The next steps in case of over-receiving may include confirming or rejecting it.
- Generate license plate: for each approved item, the system automatically generates an internal number to track this item in the warehouse and a place for storing it (putaway). WMS best practices include rules to group similar items for better storing and management.
- Quality check - report issues of Item Number (EAN): if the received item is damaged or faulty, a worker is able to report a problem by adding a photo and describing a problem.
Putaway
Once the item has been approved, the WMS app generates its license plate and determines a suggested location within the info of a specific EAN.
- Scan or enter manually EAN or license plate;
- Display info of a specific EAN;
- Confirm EAN or cancel;
- Display a suggested location;
- Confirm or cancel the suggested location;
- Check in items into racks: scan EAN or license plate and scan rack barcode/QR Code. It is used for newly arrived items and for item movement. Item check-in can also be realized with pick-to-light or pick-to-sound technology.
Inventory management
Advanced tracking and automatic identification and data capture (AIDC) systems, including RFID and barcode scanners, help warehouse managers ensure that asset inventory management can done easily.
- Search for an EAN: when entering or scanning an EAN the system displays the EAN information (item name, quantity, unit of measure/ type, size, color, SKU) and locations (racks);
- Edit EAN information.
Automated cycle count saves time and resources while minimizing the probability of mistakes. It is especially important for larger warehouses where manual cycle count is a great challenge.
- Scan or enter an EAN / license plate;
- Select quantity;
- Notification about shortage or overage;
- Edit the EAN quantity.
Outbound
Outbound features are for managing items departure from the warehouse. The worker receives the request to prepare the items for shipment with the description of the goods including EAN, license plate, quantity, time of dispatch, and destination.
- Scan or enter license plate;
- Confirm license plate;
- Generate target license plate - the number to control in the bay door location.
Labor management
Labor management helps warehouse managers distribute tasks and monitor workers' performance. Furthermore, for warehouse workers, it helps to optimize their workload and view task lists.
- User authentication, sign in and log out;
- User permission configuration;
- User work list;
- Display tasks with preview;
- Open a task page: view full task description;
- Sort tasks, e.g. by priority or by status (pending, in progress, completed, etc.);
- Manage tasks: take to work (start), pause, finish.
Reporting
Reporting tools empower managers to analyze the performance of warehouse processes and spot areas that can be improved. With properly set analytics which may also be enhanced with AI, it is possible to reduce costs, maximize storage space, and leverage seasonal inventory.
How to build a warehouse management system app?
Let’s discuss the most frequent questions related to custom warehouse app development.
How much does a warehouse management system app cost?
The cost of the development of a custom mobile application for warehouse management depends on the volume and complexity of features and integrations. Plus, it also varies due to the development agency's size, expertise, and location. The minimum project budget is about $80,000, and the average cost is between $100,000 and $300,000.
How long does it take to build a custom WMS app?
Depending on the same parameters as the cost, the duration of a WMS app development project generally takes between 5-12 months.
Factors to consider when designing a warehouse management system app
- Custom processes and maximum workflow automation by leveraging barcodes for stock management, implementing document templates, and other technologies such as battery intelligence.
- Creating a unified system with every application in it using the same records, tables, and other data which eliminates data synchronization issues and mismatches.
- Scalability of the WMS and mobile app is an important factor while every business is started with growth in mind.
- Intuitive UI to help specialists onboard easily and boost productivity.
- Qualified and experienced development team will make help you automate the processes in the right way and stay confident during the whole development journey.
- Predictive analytics to detect errors, predict stockouts and overstocking, preferences, trends, and optimize warehouse management based on this data.
Top 5 warehouse management systems
After familiarizing yourself with the cost, duration, and other factors involved in building a warehouse management system app, it's crucial to understand the key capabilities and features provided by today's leading WMS platforms.
In this section, we'll explore five leading WMS platforms that are transforming the way businesses manage their warehouses and fulfillment centers. From cloud-native flexibility to mobile-enabled efficiency, these platforms demonstrate the features, integrations, and other important capabilities that modern businesses require to thrive in the fast-paced world of warehouse management.
Cin7
📍Released: 2012.
📱Key features: Real-time inventory tracking, automated order processing, optimized storage and picking, integrated shipping and logistics, powerful reporting and analytics.
🔌 Integrations: Leading e-commerce platforms, accounting software, marketplaces, shipping carriers, POS systems, 3PL providers.
🏢 Industries: E-commerce, retail, distribution, manufacturing.
🔗 Application: Android app, iOS app
🌍 Supported Countries: Global, with customers in over 100 countries.
Cin7 is a cloud-based inventory management and warehouse management system that helps businesses streamline their supply chain operations. At the core of the platform is real-time inventory tracking and management across multiple warehouse locations, enabling companies to maintain tight control over their stock levels. The automated order processing and fulfillment workflows optimize productivity, while the integrated shipping and logistics management features simplify order fulfillment.
The platform seamlessly integrates with leading e-commerce platforms, accounting software, and other critical business systems, creating a centralized hub for end-to-end supply chain management.
ShipHero
📍Released: 2013.
📱Key features: End-to-end automation, mobile-powered workforce, seamless e-commerce integration, real-time inventory tracking, advanced reporting.
🔌 Integrations: E-commerce platforms, marketplaces, accounting software, inventory management systems, ERP systems, 3PL Integrations.
🏢 Industries: Primarily serves e-commerce businesses, including DTC brands and 3PLs.
🔗 Application: Shopify app, iOS app
🌍 Supported Countries: US, with plans to expand internationally.
ShipHero is a cloud-based warehouse management system tailored specifically for e-commerce businesses. Founded by Aaron Rubin, the platform provides end-to-end automation, mobile-powered workforce management, and seamless integration with platforms like Shopify and Amazon.
ShipHero's WMS empowers brands and 3PLs to streamline their direct-to-consumer (DTC) fulfillment operations, enabling lightning-fast shipping. In 2019, the company expanded its offerings by launching ShipHero Fulfillment, a full-service fulfillment solution. ShipHero now owns and operates warehouses across the US, serving high-growth DTC brands as well as Fortune 500 companies.
Despatch Cloud
📍Released: 2015.
📱Key features: Single API for 200+ couriers and sales channels, order/stock/warehouse management (including barcode and RFID scanning), supplier and return management, billing, and a helpdesk.
🔌 Integrations: 120+ courier integrations, including leading providers like Royal Mail, Evri, Yodel, UPS, and FedEx; 80+ sales channel and marketplace connections, including Amazon, Etsy, eBay, and TikTok Shop; accounting integrations with Xero, Sage, and QuickBooks.
🏢 Industries: E-commerce, 3PL, courier resellers.
🔗 Application: Android app
🌍 Supported Countries: UK, Germany, US.
Despatch Cloud is a cloud-based warehouse management system that provides comprehensive solutions for e-commerce and 3PL businesses. They are best known for providing efficiencies in warehouse operations and have their own testbed in their HQ building in Yorkshire with their sister companies. This boasts an impressive 250,000 sq. ft. facility where all innovations are fully tested before release.
They work closely with major couriers, retailers, fulfillment centers, and system integrators in the UK. Their products power some of the biggest fulfillment centers and retailers in the country, both on a white-label and branded basis.
Stord
📍Released: 2015.
📱Key features: Cloud-based warehouse management, real-time inventory tracking, order fulfillment, multi-warehouse and carrier optimization, predictive analytics, and 3PL (third-party logistics) services.
🔌 Integrations: Seamless integrations with e-commerce platforms, ERPs, shipping carriers, shipping & logistics, business Intelligence, enterprise applications.
🏢 Industries: Retail, e-commerce, consumer goods, wholesale, manufacturing.
🔗 Application: Shopify app
🌍 Supported Countries: US, Canada.
Stord is a reliable provider of cloud-based supply chain management solutions, offering advanced OMS/WMS technology for end-to-end, port-to-porch logistics. Stord's WMS is purpose-built by high-volume operators to drive increased labor productivity, decreased costs, and improved accuracy. With their Stord One Commerce OMS and Stord One Warehouse WMS, businesses can seamlessly connect to their Shopify stores and gain full visibility and insights to orchestrate and optimize their entire supply chain in real-time.
Stord's connectivity capabilities ensure that all supply chain data seamlessly flows between partners and systems, with easy integration with ERPs, online marketplaces, retail partners, and more. The company's robust API and EDI connectivity further enhance its ability to integrate with a wide range of systems and applications.
Logiwa
📍Released: 2013.
📱Key features: Real-time inventory visibility, intelligent warehouse automation, advanced slotting and storage optimization, seamless integrations, robust reporting and analytics.
🔌 Integrations: E-commerce platforms, accounting software, shipping carriers.
🏢 Industries: Retail, distribution, manufacturing.
🔗Application: Android app, iOS app.
🌍 Supported Countries: Global.
Logiwa is a cloud-based warehouse management system designed to help e-commerce businesses and 3PLs optimize their warehousing and fulfillment operations. Founded in 2013, Logiwa has grown to serve hundreds of customers across industries like retail, distribution, and manufacturing.
The WMS offers features such as real-time inventory visibility, intelligent warehouse automation, seamless integrations, and robust reporting. Logiwa's cloud-native architecture enables rapid deployment and scalability, while the mobile-enabled platform allows workers to access information on-the-go. Through its powerful capabilities, Logiwa helps customers increase productivity, reduce errors, and deliver a superior customer experience. The company is headquartered in Chicago and serves a global client base.
Ready to enhance your warehouse operations? Contact us today!
Contact usBottom line
Developing custom software for business automation requires a profound industry along with technology expertise. To make it right and reduce software development risks we recommend starting with discovery phase services.
At SolveIt, we provide various discovery phase packages for different business purposes. Speaking about the WMS app, the package “Business automation” is an ideal option. Contact us and we’ll share the details.